
Tailoring Shop Management
Order Management | Appointment Scheduling | Inventory Management | Financial Tracking and Invoicing | Customer Relationship Management
Streamline Order Management:
Tailoring shop management software allows you to effortlessly manage and track your orders from start to finish. With a centralized system, you can record customer details, garment specifications, measurements, and deadlines in a structured manner. The software provides real-time updates, ensuring that you can easily monitor the progress of each order, avoid delays, and meet customer expectations.
Efficient Measurement and Design:
One of the key features of tailor shop management software is its ability to store and access detailed measurements for each customer. This eliminates the need for manual measurement records and minimizes errors. Additionally, some software solutions offer design modules, enabling you to create and store custom patterns, designs, and style preferences for quick reference and replication.
Simplified Appointment Scheduling:
Managing appointments and ensuring an organized workflow can be challenging for tailoring shops. However, management software streamlines this process by offering appointment scheduling and reminders. You can easily schedule appointments with customers, allocate sufficient time for fittings, and send automated reminders to minimize no-shows and maximize productivity.
Inventory Management:
Efficient inventory management is crucial for tailoring shops. With management software, you can maintain a comprehensive database of fabrics, materials, and accessories. This helps you keep track of stock levels, reorder materials when necessary, and prevent shortages or overstocking. The software can also provide insights into popular fabrics and materials, aiding in smart purchasing decisions.
Financial Tracking and Invoicing:
Tailoring shop management software simplifies financial tracking and invoicing processes. You can generate accurate invoices, track payments, and manage expenses effortlessly. The software also provides financial reports, giving you a clear overview of your business's financial health and facilitating better decision-making.
Customer Relationship Management (CRM):
A robust CRM system is an integral part of tailoring shop management software. It allows you to maintain a comprehensive customer database, including contact information, order history, measurements, and preferences. This data helps you offer personalized services, send targeted promotions, and build strong customer relationships, ultimately driving customer loyalty and repeat business.
OUR PRODUCTS
Tailoring Shop Management
In the fast-paced world of tailoring, managing multiple orders, measurements, alterations, and customer preferences can be a daunting task. However, with the advent of tailoring shop management software, these challenges can be effectively addressed. This page explores the benefits and features of tailoring shop management software, highlighting how it can revolutionize your business operations and enhance overall efficiency.
Streamline Order Management:
Price at from 41000/- with GST
Tailoring shop management software allows you to effortlessly manage and track your orders from start to finish. With a centralized system, you can record customer details, garment specifications, measurements, and deadlines in a structured manner. The software provides real-time updates, ensuring that you can easily monitor the progress of each order, avoid delays, and meet customer expectations.
Efficient Measurement and Design:
One of the key features of tailor shop management software is its ability to store and access detailed measurements for each customer. This eliminates the need for manual measurement records and minimizes errors. Additionally, some software solutions offer design modules, enabling you to create and store custom patterns, designs, and style preferences for quick reference and replication.
Simplified Appointment Scheduling:
Managing appointments and ensuring an organized workflow can be challenging for tailoring shops. However, management software streamlines this process by offering appointment scheduling and reminders. You can easily schedule appointments with customers, allocate sufficient time for fittings, and send automated reminders to minimize no-shows and maximize productivity.
Inventory Management:
Efficient inventory management is crucial for tailoring shops. With management software, you can maintain a comprehensive database of fabrics, materials, and accessories. This helps you keep track of stock levels, reorder materials when necessary, and prevent shortages or overstocking. The software can also provide insights into popular fabrics and materials, aiding in smart purchasing decisions.
Financial Tracking and Invoicing:
Tailoring shop management software simplifies financial tracking and invoicing processes. You can generate accurate invoices, track payments, and manage expenses effortlessly. The software also provides financial reports, giving you a clear overview of your business’s financial health and facilitating better decision-making.
Customer Relationship Management (CRM):
A robust CRM system is an integral part of tailoring shop management software. It allows you to maintain a comprehensive customer database, including contact information, order history, measurements, and preferences. This data helps you offer personalized services, send targeted promotions, and build strong customer relationships, ultimately driving customer loyalty and repeat business.
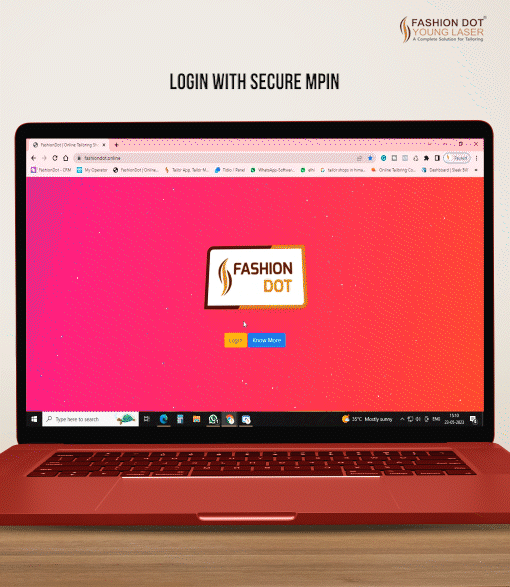

You can get all the details of your customer's orders in a few seconds
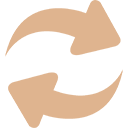